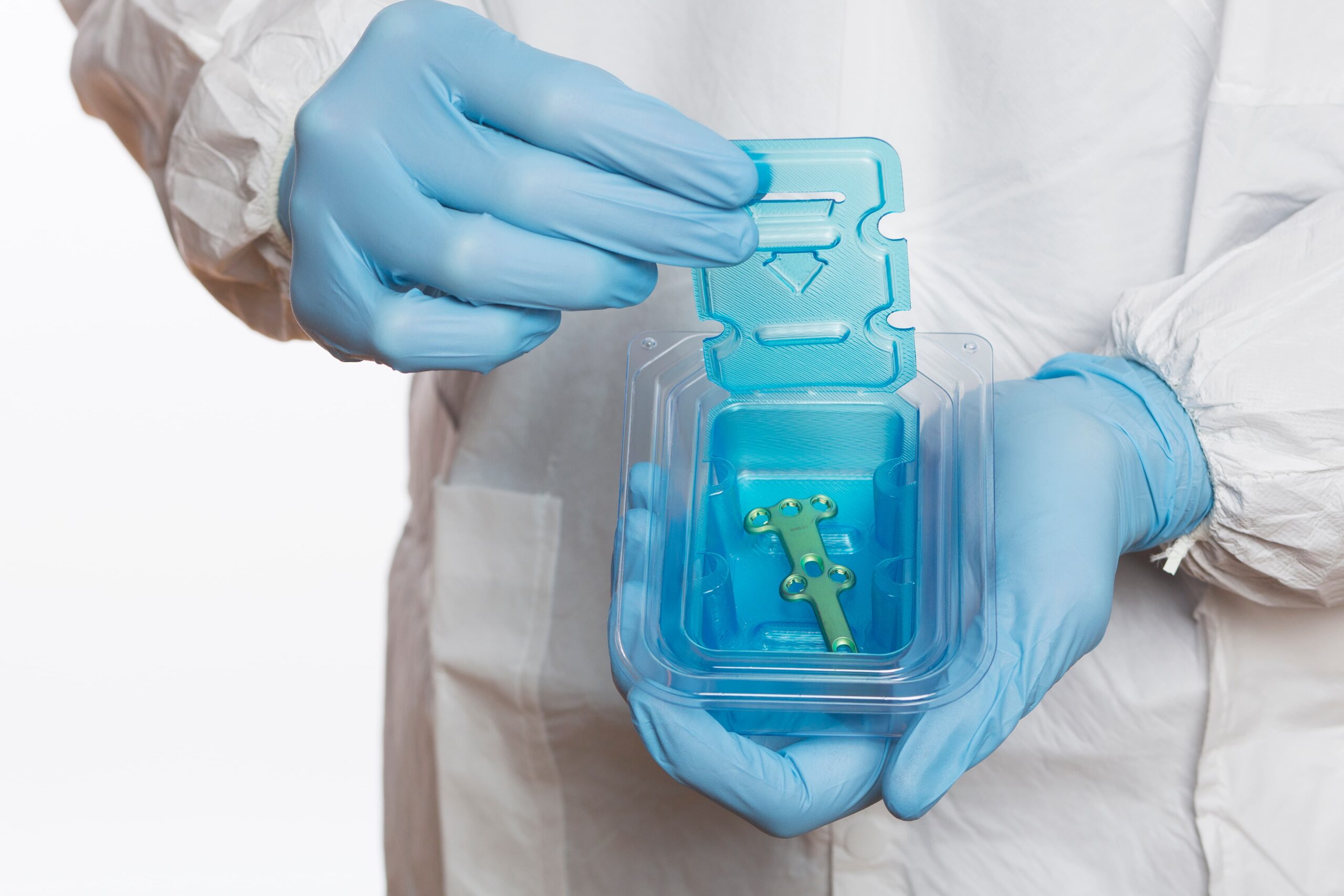
Protective & Sterile Packaging
Our solutions are made from advanced medical grade materials that are compatible with autoclave, gamma, and EtO sterilization methods. They offer sterile barrier protection along with puncture and abrasion resistance
Protection. Abrasion Resistance. Sterile Barrier Integrity.
These are important issues to ensure that your medical device, instrument, or orthopedic implant performs properly when the time comes. There can be no question as to whether your parts were damaged during shipment, came in contact with their packaging to cause particulate, or punctured the sterile barrier.
With decades of experience, access to an array of advanced medical grade materials, packaging design expertise and cleanroom manufacturing capabilities, we can partner with you to design and develop a solution that meets your exact need. Whether you need visibility of the product within the packaging, embossed part numbers, or user friendly product extraction from the sterile barrier system, UFP has the knowledge and expertise to make it happen.
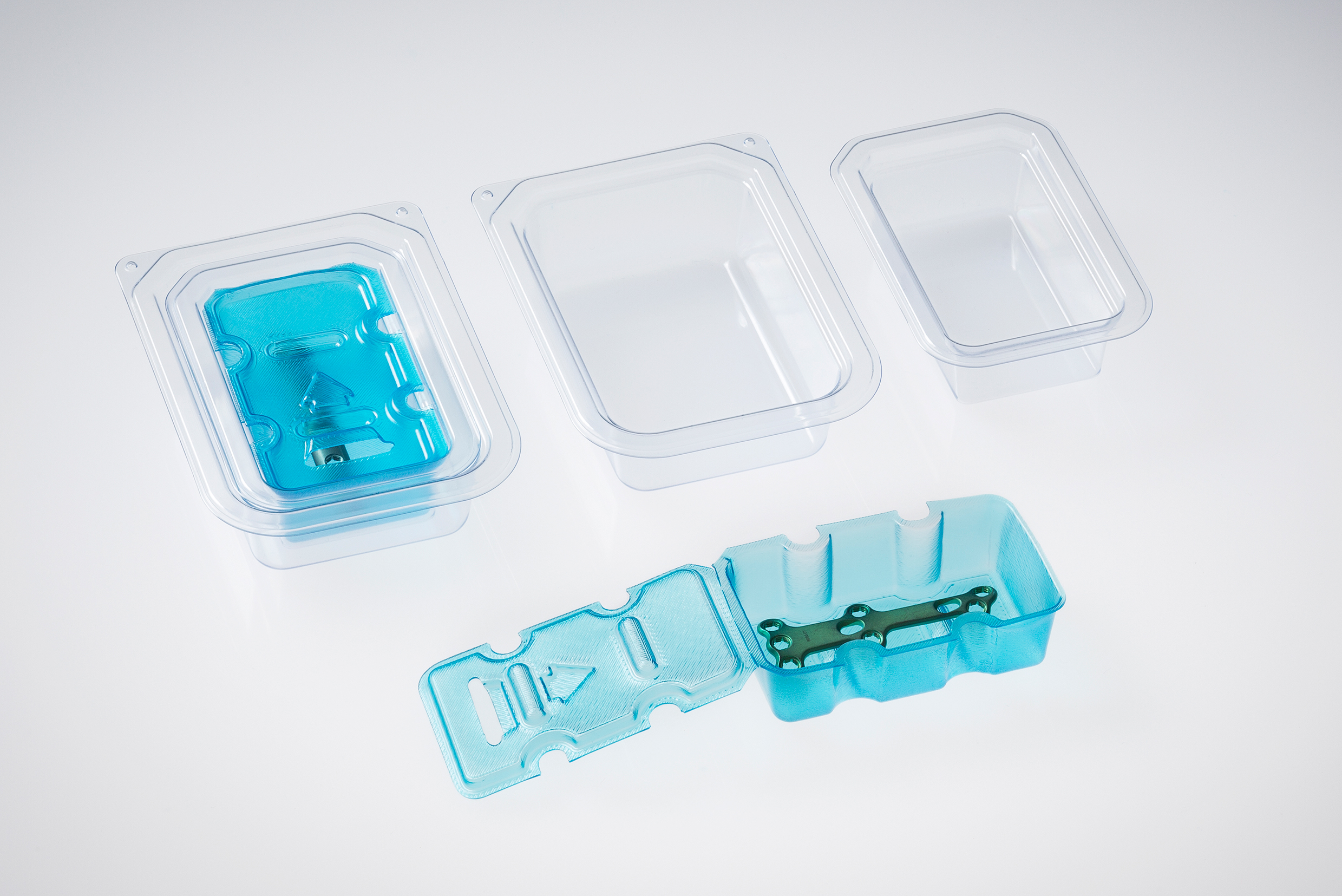
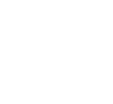
Our packaging systems can reduce tooling costs and inventory by giving you the flexibility to incorporate multiple medical products within a single package.
Sterile Protective Packaging Solutions
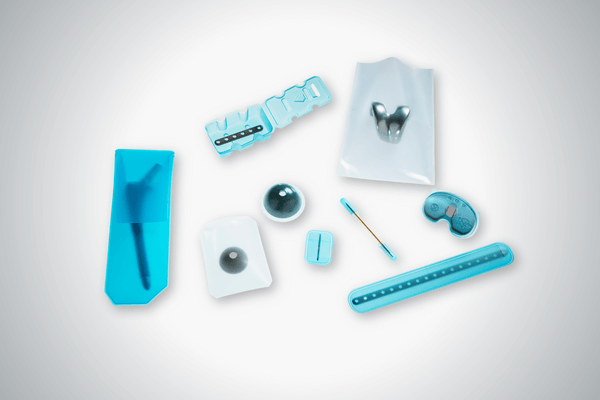
FlexShield® TPU Packaging
FlexShield is a flexible thermoplastic polyurethane film used for medical packaging, component, and product applications. Its durability and sterility lend itself to providing excellent protection for devices and patients. In addition to custom FlexShield solutions, we offer standard FlexShield pouches, bags, and tip protectors.
Utilizing FlexShield within your packaging systems will ensure the integrity of the sterile barrier between your instruments and outside contaminates.
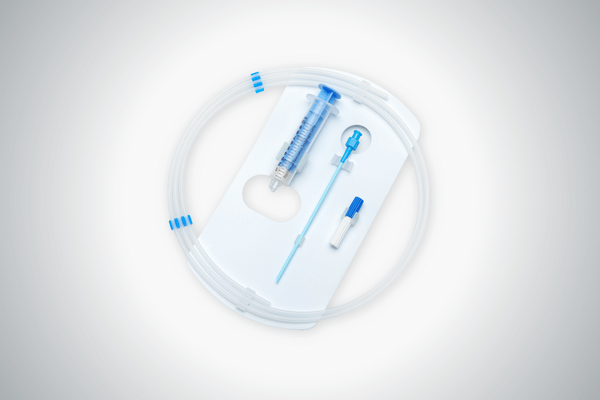
EZ-Card® HDPE Packaging
Elevate your medical packaging with our thin, lightweight, and recyclable high-density polyethylene (HDPE) EZ-Card. Also known as backer cards, mounting cards, HDPE cards, die cut inserts, or insert cards, EZ-Card is designed to safely and securely hold medical instruments and devices utilizing retainment features such as EZ-Clip™ injection molded clips and die cut tabs, slots, folds, and straps.
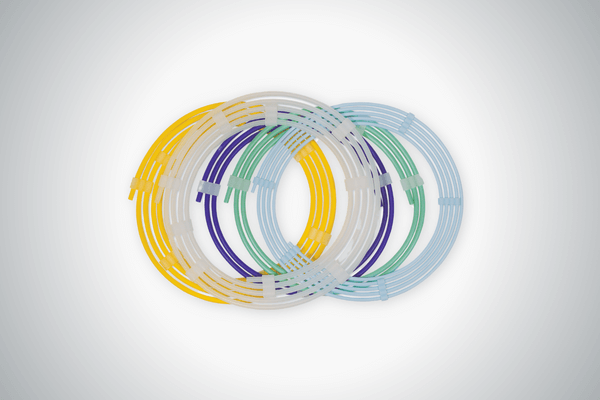
Catheter & Guidewire Dispenser Coils
Dispenser coils are used to safely protect catheters and guidewires during storage and shipping as well as facilitate aseptic presentation and deployment during surgical procedures.
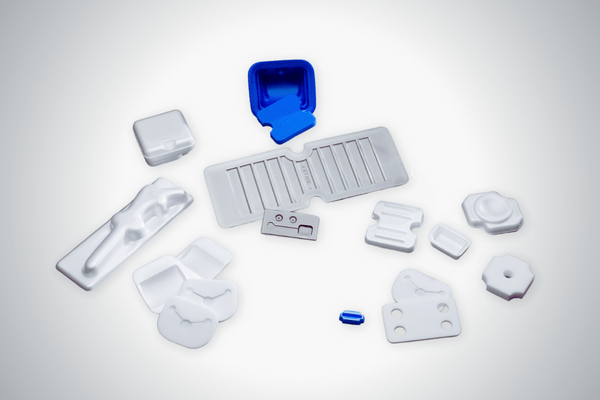
Medical Grade Foam Packaging
UFP MedTech has access to an array of medical grade closed-cell and open-cell foams, which are commonly used for medical instrument packaging in the form of trays, inserts, and pouches. Many of these foams are compatible with autoclave, EtO and gamma sterilization methods.
We offer closed-cell foams that are manufactured with nitrogen to eliminate out-gassing allowing the packaging to be used in operating rooms and cleanroom environments.
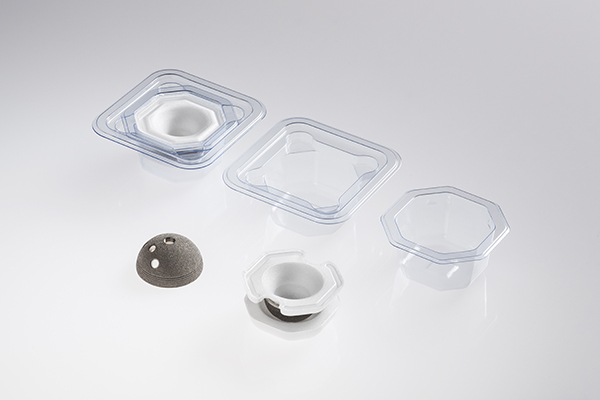
Rigid Plastic Packaging
PETG, PETE, ABS, HDPE are commonly utilized thermoplastics for medical device packaging due to their durability and ability to withstand sterilization. Rigid plastics can be vacuum formed into clamshells, trays, and components used for protective packaging, procedure kits, and medical trays.
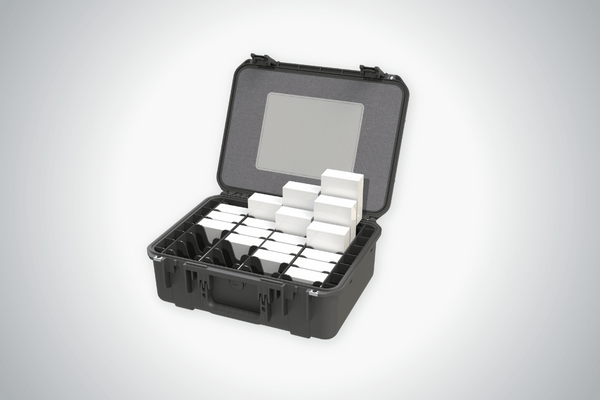
Protective Cases
For decades, UFP MedTech has been an industry pioneer in the design and development of case and insert solutions for high value and fragile medical products.
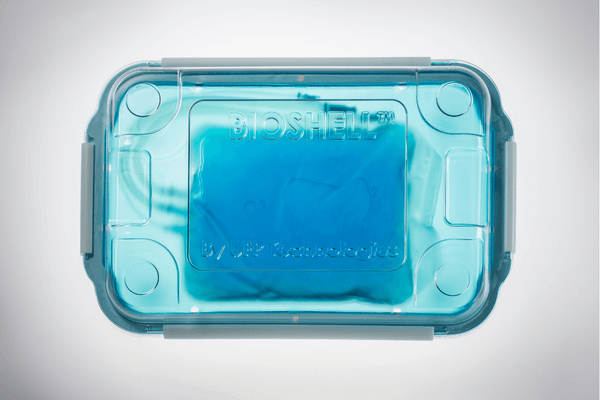
Bioprocess Bag Protection and Insulated Shipping Containers
Our BioShell® system has become the biopharmaceutical industry’s most trusted solution to provide maximum protection for frozen single-use bioprocess bags. BioShell improves bag protection through our unique suspension system that mitigates the risk of bag damage during storage, handling, and transport.
To keep BioShells and other bioprocess bag container systems frozen during transportation we’ve developed CryoShell®, an advanced insulated shipper designed to keep contents stored as low as -80°.
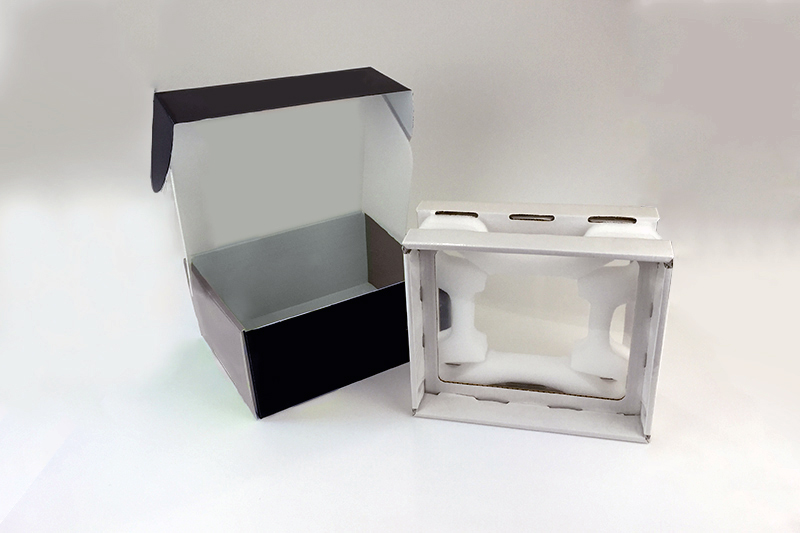
Allograft Packaging
At UFP MedTech, we strive to offer quality packaging solutions that address our customers’ main concerns. In the allograft packaging space, this includes using materials that protect an implant being transported to the operating room, while maintaining proper temperatures for up to 120 hours.
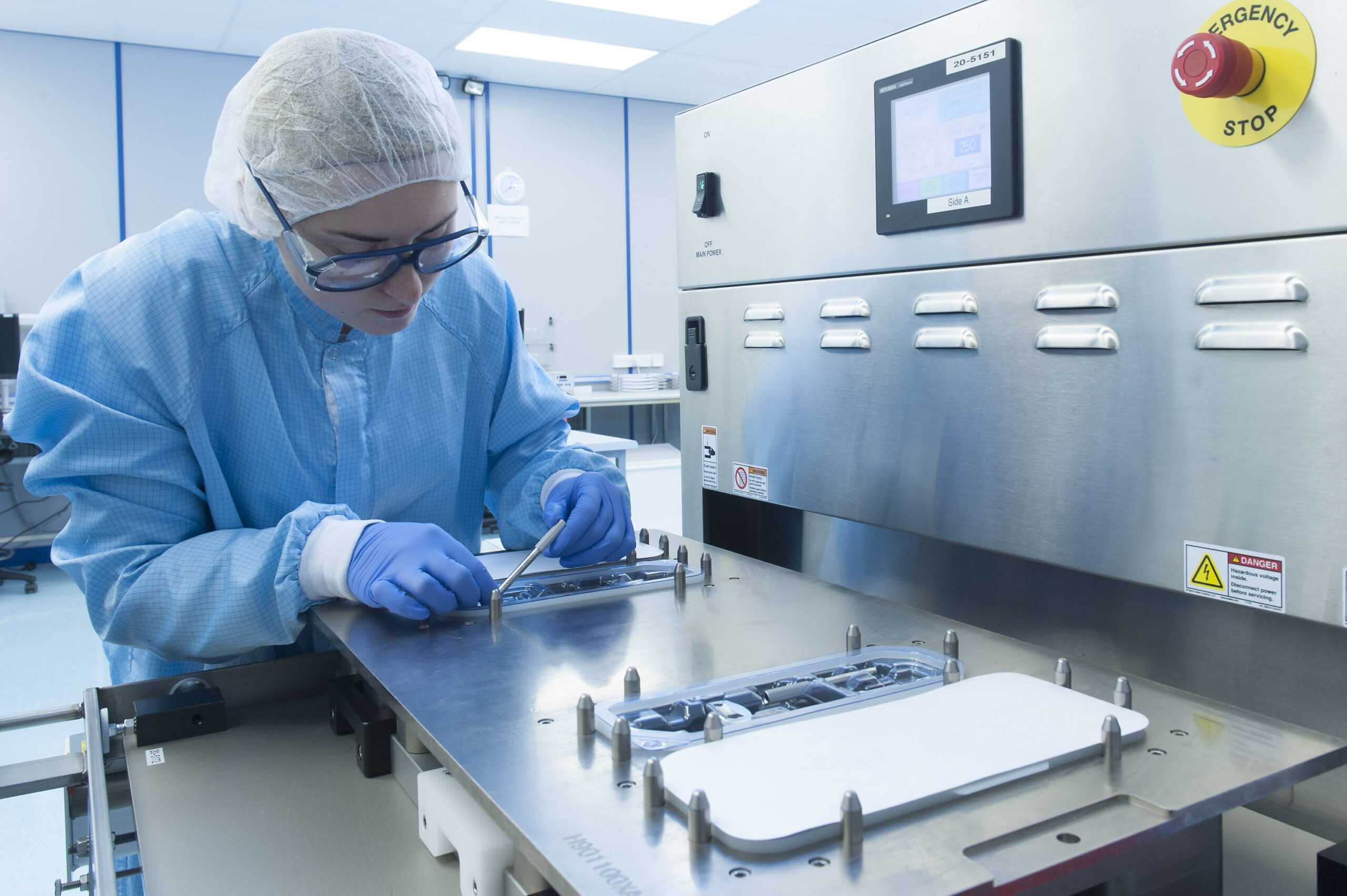
Request a Consultation
Whether you need a partner for one phase of development, or all phases from design through manufacturing, our team of experts can guide you every step of the way.