Packaging for medical devices is not just for holding product. It performs many other critical functions such as protecting from damage during shipping, storage, and handling, while allowing for sterilization, maintaining sterility, providing product identification, label readability, and ensuring correct usage during aseptic presentation.
According to the Sterile Barrier Association, the packaging around medical devices that allows those devices to be sterilized, provides a microbial barrier, and maintains sterility effectively up to the point of use is known as a Sterile Barrier System (SBS). Packaging designs should incorporate all aspects of usability while preventing microbial contamination.
EN ISO 11607-1 defines aseptic presentation as the introduction and transfer of a sterile product using conditions and procedures that exclude microbial contamination and specifically peel-open characteristics of the SBS shall be continuous and homogeneous, without delamination or tearing of the material that can affect aseptic opening and presentation. This must be designed into the system.
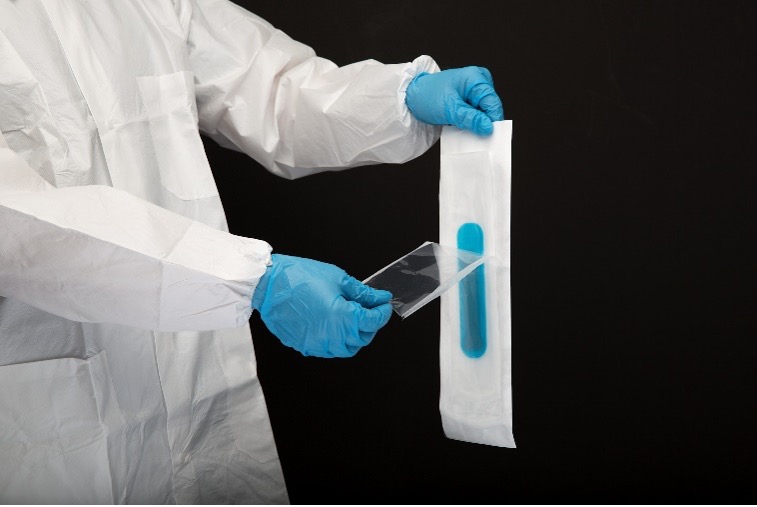
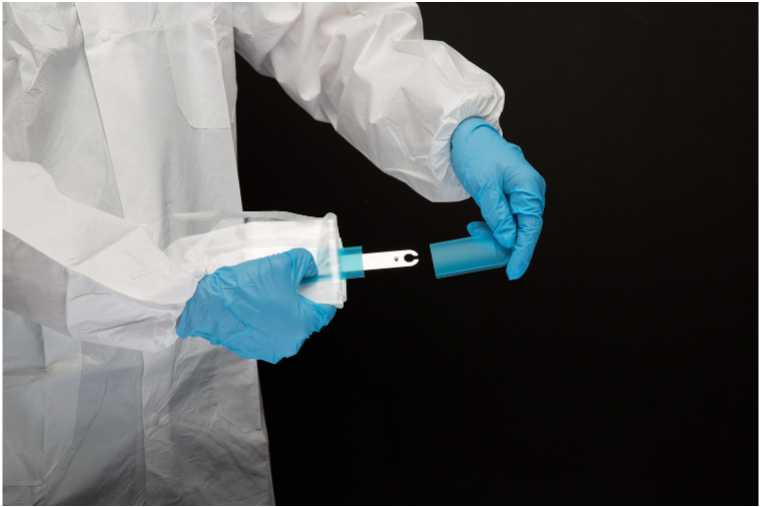
Improvements in Medical Packaging
For over 35 years, UFP MedTech has been at the forefront of sterile packaging technologies that address the continually evolving requirements of performance, safety, weight, and size. Our solutions range from moldable and durable film-based packaging to catheter and guidewire packaging to mounting cards with integrated clips to securely hold large and heavy devices. The following illustrates the development, evolution, and use cases of our three most popular materials for sterile barrier medical packaging.
FlexShield® Sterile Packaging: A Safer and Higher Performing Alternative
UFP MedTech’s FlexShield was developed to address multiple material issues with PVC which was commonly used for orthopedic packaging of delicate products. PVC contains plasticizers which are not stable, leach out over time, and transfer to the medical device (e.g., implant). In addition, PVC can particulate from abrasion, and become punctured from sharp devices. Lastly, implant manufacturers were looking to improve aesthetics and ease of use.
In 2001, UFP introduced FlexShield medical packaging, made from thermoplastic polyurethane (TPU) which at the time was commonly used in the footwear industry. This material is made from a USP Class VI resin, is FDA approved, and compatible with EtO, gamma, and electron beam sterilization processes. Additionally, TPU is abrasion and puncture resistant and can be molded into custom shapes. FlexShield pouches and tubs can also incorporate ease of use features such as grips and instructions, while ensuring aseptic presentation. Today, UFP MedTech uses FlexShield in all of our pouches, tip protectors, tubs, and bags.
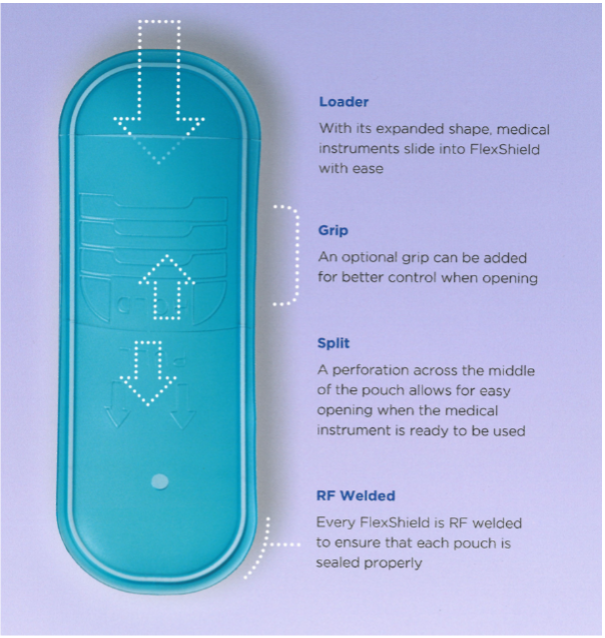
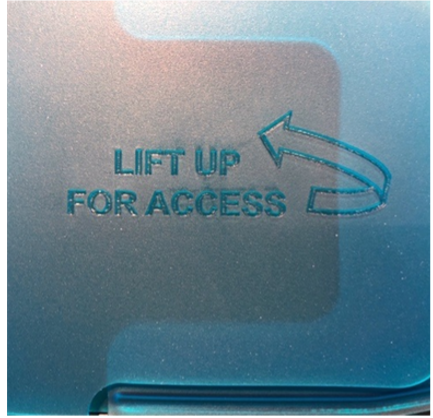
Examples of ease of use features such as embossed instructions, perforations, and grips
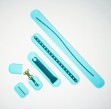
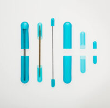
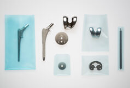
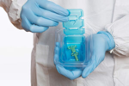
FlexShield pouches, tip protectors, tubs, and bags
Catheter & Guidewire Dispensers: Inventing an Industry Standard
In 1987, Ray Byrnes was in the Tyvek business. His customer Bard had complained that the opening and handling of coiled guidewires in the ER was a two-person job to make sure sterility wasn’t compromised. To address this issue, he developed the industry’s first dispenser coil and Contech Medical was born. He even built custom machinery to produce them. In 2005, Contech Ireland split from Contech Medical to form Advant Medical. Today, both companies are part of the UFP MedTech family and together they are the largest producer of catheter and guidewire dispenser coils globally.
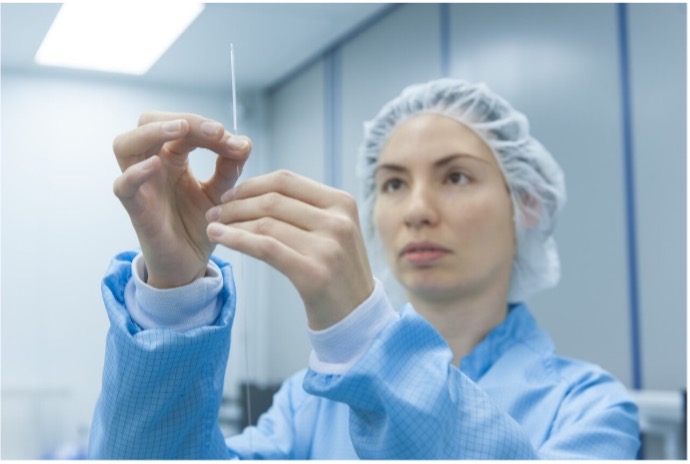
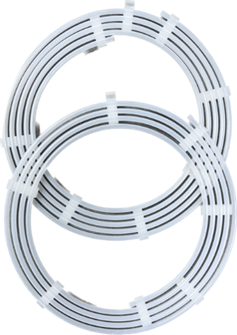
Catheter and guidewire dispenser coils are typically made from polypropylene (PP) tubing and held in place with injection molded clips. Each coil is a custom length and diameter based on the size and length of the catheter or guidewire. Once loaded, the coil is packaged and sterilized. For over 35 years, this design is still the gold standard in ease of use, aseptic presentation, and sterility.
EZ-Card® HDPE Packaging: The Next Generation in Backer Cards
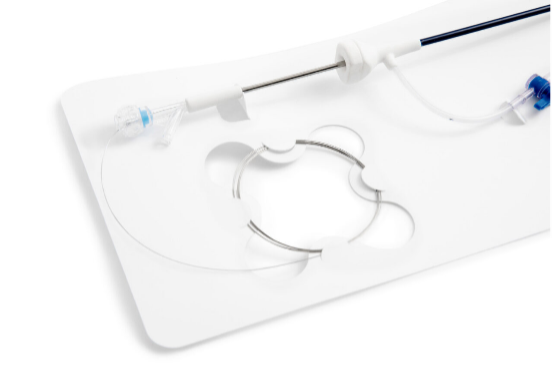
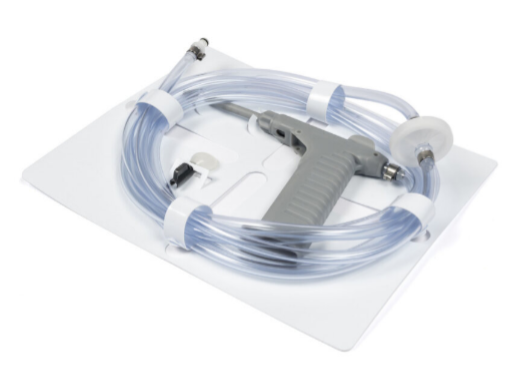
EZ-Card, also known as backer cards, mounting cards, HDPE cards, die cut inserts, or insert cards, are designed to safely and securely hold medical instruments and devices utilizing retainment features such as our proprietary EZ-Clip injection molded clips as well as die cut tabs, slots, folds, and straps. EZ-Card is an excellent and cost-effective alternative to bulky rigid trays and other medical packaging options. They are used to position and secure medical instruments and devices within a sterile barrier package to ensure sterility throughout the supply chain. Due to their thin, flat, flexible design, mounting cards pair easily with Poly/Tyvek pouches to provide a double barrier packaging system. Additionally, EZ-Card can reduce the overall size of the SBS, is light weight, and can ship and store flat.
Various Retainment Options Are Available
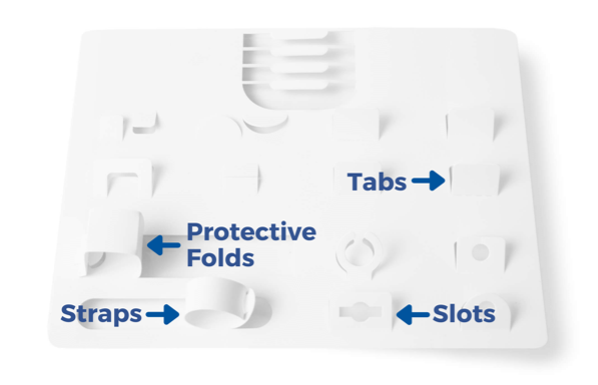
UFP MedTech recently introduced EZ-Clips which utilize injection molded clips instead of die cut retainment tabs to secure large or heavy devices. A variety of clip sizes are available and are faster to assemble than traditional cards where the tabs must be “popped” up individually prior to loading. Devices are held more securely and therefore aseptic presentation is improved as well as ease of removal from the card.
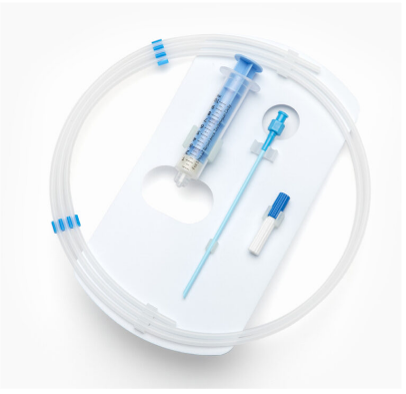
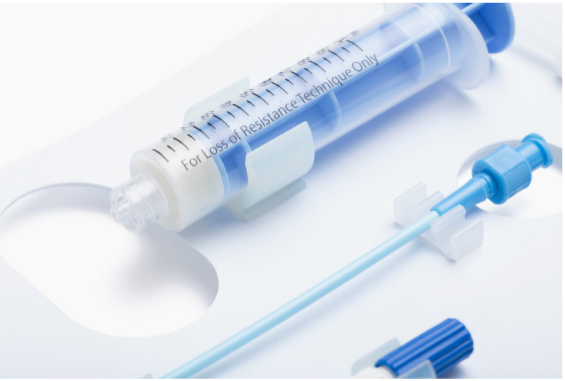
No matter the sterile barrier system you use for your device, ease of use and fail-safe aseptic presentation is crucial to minimizing the chance of contamination due to a packaging design not optimized to the device’s specific geometry and intended use in the operating room.
To learn more about UFP MedTech’s sterile packaging systems, contact our team to get started.