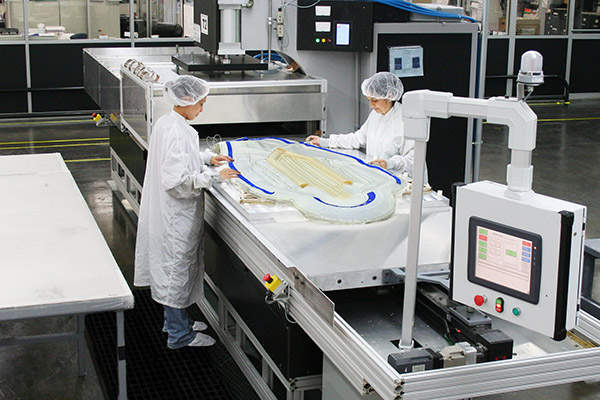
Applications
- Sleep Surfaces
- Wound Care
- Protective Packaging
- Temperature Management
- Laparoscopic Devices
- Medical Balloons
UFP MedTech brings decades of expertise in the welding and bonding of engineered thermoplastic materials for the manufacture of medical devices, sub-assemblies, components, and packaging. This includes radio frequency, impulse, ultrasonic, and thermal welding.
Specifically, UFP MedTech has a particular expertise in radio frequency welding (also referred to as RF welding, dielectric sealing, high frequency welding, or heat sealing), a technology that uses electromagnetic energy to form a permanent bond that is as strong as the original thermoplastic materials.
What Factors Contribute to a Good Weld?
Many factors affect the strength and seal quality in thermoplastic welding. Tooling layout, weld thickness, material thickness, and machine control are some of the most important factors in creating a good seal. The appeal of thermoplastic welding is in the completeness of the weld. Using this method can create very robust hermetic seals. Many welds are subject to pull tests, leak tests, and optical tests to determine that the correct conditions have been achieved.
What Materials Can Be Thermoplastic Welded?
Some materials are more of a challenge to weld than others and may even require a special process. No matter the level of difficulty, UFP MedTech is confident in its ability to expertly perform welding on the following materials:
Why Use RF Welding?
There are several alternatives to RF welding including sewing, gluing, or using hot air. Why use RF welding?
RF Welding vs. Sewing
RF welding provides a consistent air and liquid tight seal unlike sewing. When sewn seams are stressed, the thread takes the pressure and could break. RF welds evenly distribute stresses throughout the material providing a much stronger seam while preventing any air, moisture, or debris getting in.
RF Welding vs. Gluing/Adhesives
Gluing can provide an air tight solution, but gluing takes much longer than RF welding and often uses hazardous solvents that are harmful to the environment. Glued seams are also subject to failure once the adhesive has worn out.
RF Welding vs. Hot Air
Hot air is a method that applies heat to the outside of the material to melt it and create a bond. This method is only effective up to certain thicknesses. Materials that are too thick will not bond in the middle as the core will struggle to melt, while the outside layers are over heated or burned. RF welding heats from the inside out and is the best method for forming air tight seams.
UFP MedTech’s RF Welded Products
Our packaging pouch made from FlexShield® thermoplastic polyurethane film (TPU) is manufactured via RF welding and provides puncture and abrasion resistance in order to safely ship medical instruments without incurring damage to external packaging. Utilizing FlexShield pouches within your packaging systems will ensure the integrity of the sterile barrier between your instruments and outside contaminates.
RF welding is also used in a number of other applications including:
To request a consultation, contact us below or give us a call at 866-921-4718
* denotes mandatory fields.