As one of the leading medical foam fabricators in North America, UFP MedTech has the knowledge and expertise required to select the optimal materials for medical products comprised of foam.
Choosing the proper foam material for a medical application can be a very challenging task. Not only do different foams have varying cell structures and characteristics, but foams from the same material family can also be made with vastly different density and firmness specifications that will greatly affect their performance. We’ll work with you to determine the characteristics you need to make your packaging or product perform as intended.
Below are the most common foam definitions we use to help select the correct material for your project:
- Biocompatibility
The foam has been tested, passed and certified to comply with the ISO 10993 protocol. - Fixed Formulation
The raw material formulation may be registered with the FDA. Should the material change, it is determined that the foam is not able to be categorized as a medical grade foam without additional testing. - FDA Master File
This is where foam formulations are registered with the FDA. It is important to remember that a foam with an FDA master file means that the formulation is registered with the FDA. It does not necessarily mean that the foam is “medical grade.” Additional biocompatibility testing will determine whether or not the foam is appropriate for use in medical applications. - 510K Submissions
We will work with the raw material supplier and customer to determine if the foam has previously been registered in a 510K application. - USP Classification
This is a raw material registration used primarily in the pharmaceutical industry.
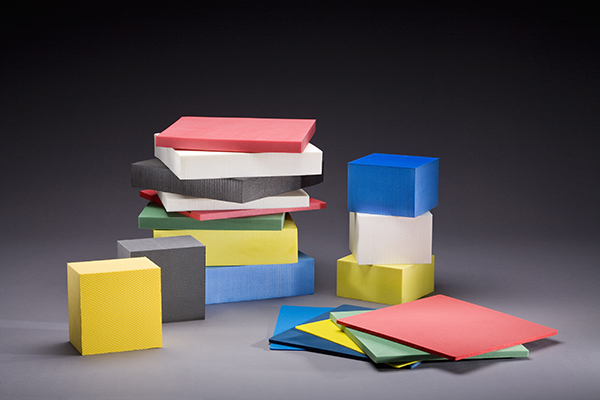
Closed-Cell Foams
Closed-cell foams such as polyethylene foams and cross-linked polyethylene foams are commonly used for medical device packaging and component solutions.
Cross-linked polyethylene foam (XLPE)
Cross-linked polyethylene foam (XLPE) is a closed-cell foam characterized by a compact feel and resistance to water. It has many of the same properties as polyethylene foam but also has the ability to protect Class “A” surfaces and is consequently used extensively in the packaging of medical products and equipment.
UFP MedTech utilizes XLPE foams that are impregnated with nitrogen providing a non-toxic, hypoallergenic, latex-free solution that can come in direct contact with skin and be used in operating rooms.
Compression Molding is often used when creating components, packaging and products from closed-cell XLPE foams. This fabrication method provides a unique finish that is aesthetically pleasing while still providing the necessary cushioning and support required.
Polyethylene foam (PE)
Polyethylene foam (PE) is a durable, lightweight, resilient, closed-cell material. It is often used for packaging sensitive instruments and devices due to its excellent vibration dampening and insulation properties. It also offers high resistance to chemical and moisture.
PE foam is easy to process and fabricate. It has high load bearing characteristics that help manufacturers reduce packaging costs as they can use thinner and smaller amounts of foam yet still protect their products.
We use these materials in solutions ranging from:
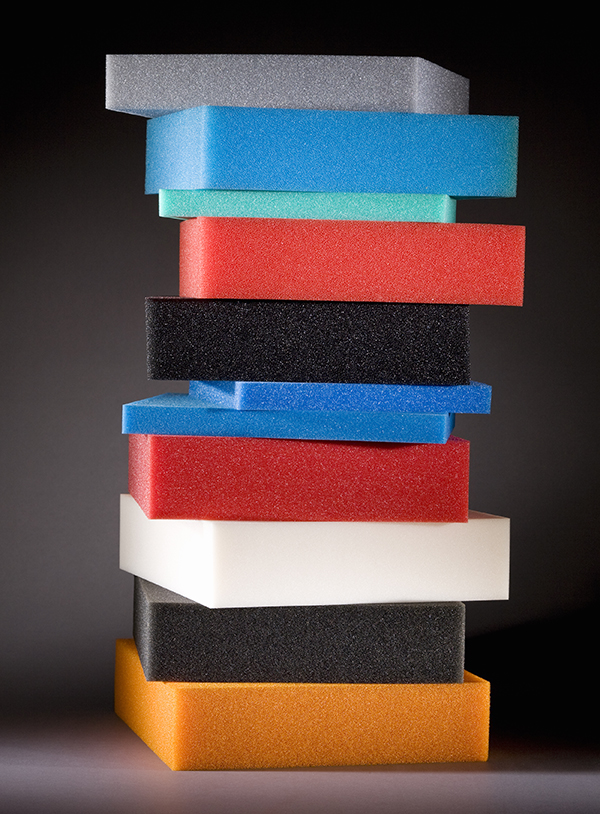
Open-Cell Foams
UFP MedTech utilizes a range of medical grade open-cell foams such as polyurethane and reticulated polyurethane foams that are frequently used for various medical applications and packaging solutions.
Polyurethane foam (PU)
Polyurethane foam (PU) is characterized by its light weight, resiliency, low odor and high resistance to mildew. It provides excellent cushioning and is used extensively in applications such as bedding.
This open-celled foam is used regularly in medical packaging where abrasion resistance is required. It is available in two primary types, polyether and polyester, in a range of densities and colors.
Reticulated polyurethane
Reticulated polyurethane foam is used extensively in the medical industry as it is easy to clean, impervious to microbial organisms, and can be made with fungicidal and bactericidal additives for added safety. Reticulated polyurethane foams can even be injected with substances to achieve other unique properties.
It’s typically used to make products that are involved in filtration, sound absorption, fluid management, wiping and padding. This family of materials features high tensile, elongation and tear characteristics.
We use these materials in solutions ranging from:
To request a consultation, contact us below or give us a call at 866-641-0560
* denotes mandatory fields.